Condition Monitoring and Remote Vibration Analysis
for troubleshooting support or condition-based maintenance (CBM) applications
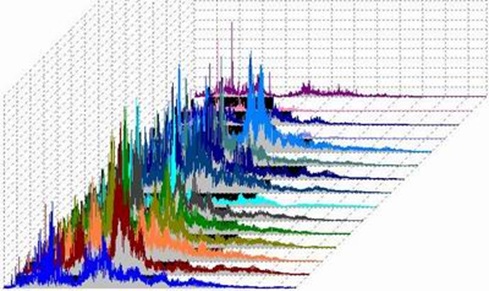 |
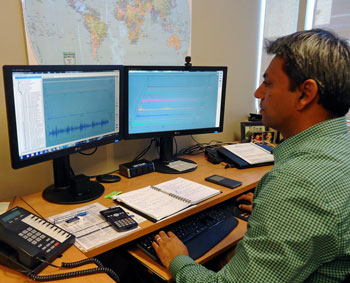 |
Remote vibration data analysis can help diagnose problems efficiently, especially for production facilities in remote locations.
|
In the many cases where it may not be feasible (or cost-effective) to have your own vibration expert at site or if you need some initial advice before having Wood come to site, an easy solution is to have the equipment owner (or operator) send vibration data to Wood for analysis. One of Wood’s knowledgeable analysts will identify locations where testing should be done, and if required, can provide a simple data collector or test equipment. The data can be emailed to Wood VDN, allowing for fast review and analysis. We will evaluate the results and discuss options with the equipment owner or operator.
Speak to a specialist
1 Overview
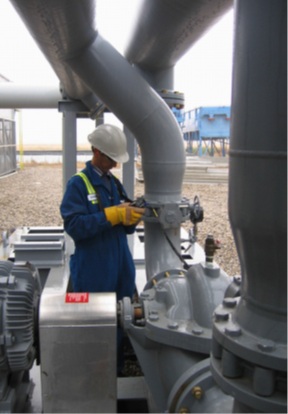 |
Collect vibration data and
email it to Wood for analysis |
- Ideal for production facilities with no vibration experts on site
- Cost effective for initial troubleshooting support or for more routine analysis
- Customers simply collect vibration data and send it to Wood VDN for analysis
- VDN analyzes the data and provides recommendations
- The program is flexible to suit customer needs; i.e., it can monitor intervals of critical and auxiliary machines, and is designed to fulfill your maintenance strategy requirements
2 Scope
2.1 Troubleshooting Assistance
If you have a vibration problem and want some preliminary advice before calling Wood VDN to site, then this service may be a good solution.
- Contact Wood VDN to review the situation.
- Establish the initial budget and authorize VDN to proceed with the initial review (e.g., purchase order for office support).
- Arrange for data collection equipment (Wood to coordinate and send a suitable data collector or client to provide).
- Define measurement locations, test plan, and testing support.
- Collect and send vibration and other data to VDN for review and analysis; VDN works collaboratively with you to assess problems and recommend next steps.
2.2 Routine Monitoring Program
If you would like to set-up a regular monitoring program, Wood can help coordinate and manage the program. This could apply to a condition monitoring program involving critical and less critical machines (compressors, pumps, motor bearings, turbines, etc.).
- You identify equipment to be monitored. If you like, we can provide suggestions regarding equipment and how often to monitor.
- When you are ready, a VDN professional visits your site to help you get started with a short training session on using the data collector, marking the test locations on your equipment, and planning your route.
- We help you collect and email your first set of data to VDN.
- We can also provide a short seminar to your maintenance, operations, and rotating staff on vibration analysis and machinery troubleshooting.
3 Wood Advantages
3.1 Expert Analysis and Support
- You can rely on VDN. With more than 50 years of vibration experience, we are global leaders in vibration analysis for compressors, pumps, and rotating equipment.
- This service applies to any reciprocating or rotating equipment– anywhere in the world.
- Our experts have a proven process to analyze your data. Here’s what we do:
- Evaluate overall vibration readings, a wide spectrum of frequencies, envelope, and bearing defect vibration readings.
- Track the change in vibration over time and compare to industry standard guidelines.
- Compare results across similar classes of machines.
- Use advanced algorithms to identify emerging problems.
- Track operating parameters (pressures, temperatures) to correlate vibration levels to operating conditions.
- If a problem is identified, we contact you. We send you alarms or alerts, discuss the situation with you, and include recommendations.
- You get summary reports containing recommendations for, and an overview of, your machinery assets including a risk‐based action summary, so you can focus action where it’s needed the most.
- Detailed machine data can be sent to you on request.
- Should a problem occur, Wood can provide additional troubleshooting support.
3.2 Benefits
- Cost effective
- Saves money – no need for certified vibration analysts on site.
- Saves time – plant personnel can collect data when needed.
- No capital investment – a simple monthly or quarterly fee per machine.
- Improved equipment reliability, safety, and lower maintenance costs.
- Provides excellent results by combining plant personnel knowledge with Wood’s vibration expertise.
3.3 Example
This chart shows the vibration data for a centrifugal pump. Each measurement point is added to the previous trend and the most recent event is on the bottom. As confirmed by the data collected, the pump had a history of low vibration levels. After a mechanical seal change, VDN noticed that the vibration amplitudes at 150 Hz (twice rotational speed) doubled, generating an alert. VDN determined the cause to be a severe shaft misalignment and contacted the client, recommending hot alignment of the pump and turbine. After the alignment was performed, the vibration was reduced to baseline levels, and the 2 times spectrum peak was eliminated, significantly extending the mechanical seal life and avoiding costly downtime.
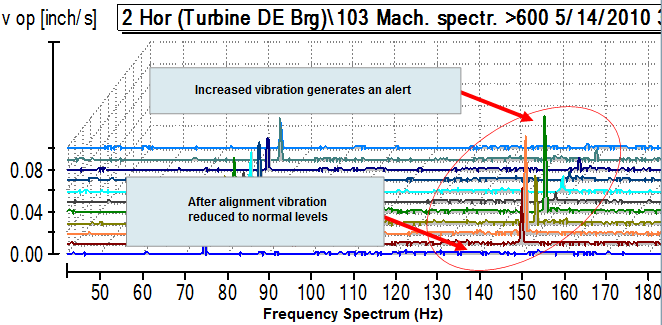
4 Representative Examples
5 Related Services
6 Keywords
- Condition Monitoring
- Condition Based Maintenance
- Performance Monitoring
- Equipment Reliability
- Remote Vibration Analysis
- Remote Vibration Monitoring
- Outsource Vibration Analysis
Back to top
Free webinar
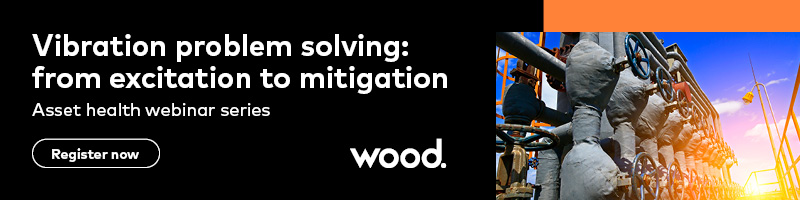
Understand the top three vibration threats in your piping system and how to tame them. Register now