Torsional Vibration Analysis (TVA)
A torsional study evaluates crankshaft, coupling, and gears to ensure torsional vibration is acceptable.
Wood’s vibration experts use our field-proven proprietary simulation software to:
- Conduct a modal analysis of the mass elastic model to determine Torsional Natural Frequencies (TNFs),
- Assess the torque effort curves for all key operating conditions,
- Perform a forced response analysis to accurately predict torsional vibration and stress, and
- Recommend solutions to ensure a safe torsional system.
Unique features offered exclusively by Wood to ensure a more reliable system include:
- Analysis with Wood’s DataMiner™ tool yields advanced analytics and design sensitivity.
- Torsional Vibration Analysis integrated with the Pulsation and Mechanical Vibration Analysis ensures superior study results.
- Determination of risks due to lateral frame forces caused by torsional responses in reciprocating compressors and integration with Wood’s Mechanical Vibration Analysis results in lower probability of vibration.
Speak to a specialist
1 Background
Excessive torsional vibration and resonance leads to damaged crankshafts, couplings, gears, auxiliary equipment, and more. Examples of damaged couplings and shafts are shown below. Repair costs to such equipment can easily exceed $1,000,000 in parts, labor, and downtime.
Over 80% of all torsional systems we analyze require system modification during the design stage to reduce the risk of failures.
Torsional vibration will vary depending on the system’s characteristics and the specific operating conditions (torque effort curve). Any changes to these factors can result in excessive torsional vibration.
For an overview of torsional vibration, we recommend viewing this short video:
For more information, training or support, contact Wood.
 |
A) Motor Failure B) Damaged Coupling C) Fractured Shaft D) Melted Rubber Coupling
|
2 Applications and Tips
The drive trains in the following applications require a Torsional Vibration Analysis:
- Reciprocating Gas Compressors
- Screw Compressors
- Plunger and Centrifugal Pumps
- Centrifugal compressors
- Engine/Generator Sets
Tips for Improved Torsional System Design
A TVA should be performed for:
- Any new combination of driver/driven equipment
- Any change in compressor configuration (different cylinders) or significant changes in operating conditions (pressures, cylinder loading).
- Different motor (same frame rarely means same rotor inside)
- Drive trains experiencing failures
- VFD applications
- Sensitive and critical systems
Note: a field assessment is recommended to confirm torsional vibration and dynamic stresses.
3 Scope
The following scope is standard in Wood’s torsional studies. The scope is compliant to API studies, including but not limited to 610, 613, 618, 671, and 684.
Performance Assessment:
- Assess the overall operating envelope to accurately determine the worst case conditions
- Include upset and startup cases if applicable
Modal Analysis:
- Generate the mass elastic model for the entire drive train
- Calculate the torsional natural frequencies and mode shapes
Forced Response Analysis:
- Calculate the vibratory torque acting on the system
- Perform the forced response analysis to assess torsional vibration and dynamic stress amplitudes
Torsional to Lateral Excitation (Reciprocating Compressors):
- Calculate the lateral frame forces induced by the torsional vibration of the crankshaft
- Assess the risk based on magnitude of lateral forces
- Coordinate with Wood Mechanical Vibration Analysis to avoid mechanical resonance
Motor Electromagnetic Effects:
Data Visualization and Quality Checks:
- DataMiner™ software tools are used to assess the system and compare alternatives; can visualize results across hundreds of operating conditions
- Technical review performed to ensure validity of model and inputs
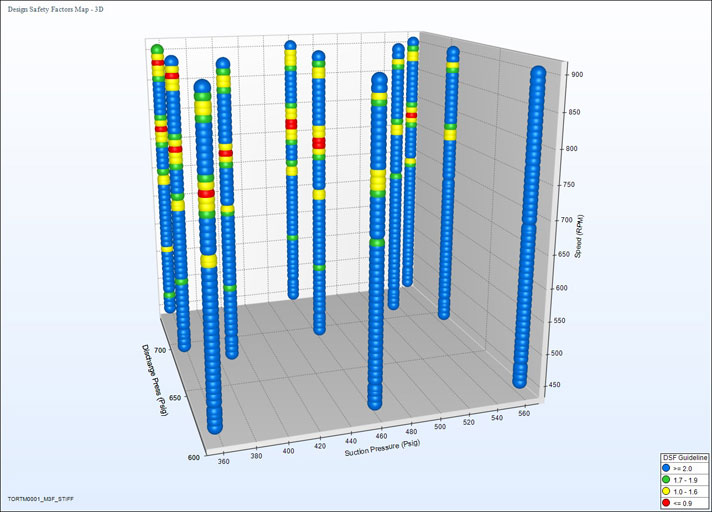 |
DataMiner™ – a unique analysis tool to view the overall results in many different ways (e.g., Motor Shaft Design Safety Factor).
This tool allows the customer to evaluate the vibration risks across all of the analyzed operating conditions. RED indicates areas that must be avoided, or else failure will occur. YELLOW indicates areas that are marginal and should be avoided. Each circle is a unique combination of operating condition and speed analyzed in the study. DataMiner is a proprietary feature for Wood’s clients.
|
Recommendations:
To avoid torsional resonances and excessive torsional vibration we recommend changes such as, but not limited to:
- Coupling type, model and size
- Flywheel installation
- Detuner installation
- Limiting operating conditions and/or speed
- Material changes to the shafts
4 Options
- Crankshaft Analysis – Wood calculates the mass-elastic data for a crankshaft if that data is not available
- Balance Analysis – the unbalanced forces and moments for a reciprocating unit are calculated. Recommendations will be made to change balance weights if necessary.
- Finite Element Analysis – Wood can perform a detailed three-dimensional stress analysis for new crankshaft designs. FEA
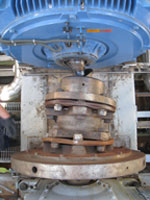 |
|
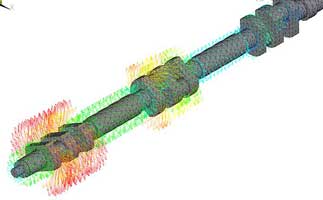 |
Broken shaft – resulted from a Torsional Analysis with limited conditions
|
Three-dimensional finite element model of a 6 throw compressor crankshaft – used to calculate mass-elastic data for a Torsional Analysis
|
5 Wood Advantages
- Comprehensive evaluation of the entire range of operating conditions plus upset conditions – not just the assumed "worst case." This improves system reliability and avoids the chance of design errors.
- Wood’s tolerance band analysis improves accuracy and minimizes risk. This technology evaluates the risk and design impact due to the tolerances of key input parameters. Wood’s approach reduces the risk of failures and avoids unnecessarily expensive torsional solutions.
- Wood has an extensive database of engine, motor, compressor and coupling information – resulting in faster and more accurate analysis.
- Our system approach focuses on the entire package including engine, driver, coupling, etc. This approach is more comprehensive and accurate compared to services that focus primarily on the engine (or compressor).
- Full service including integrated design of torsional, pulsation, and mechanical systems. This enables effective solution to torsional/lateral excitation, coordination between pulsation changes and torsional impacts.
- Proprietary software tools for more accurate, faster, and advanced features (Torsan™, RCA™, and DataMiner™).
- Technical review for improved quality control. Industry leading technical experts are involved on your project to avoid problems or errors.
- Dedicated torsional support team that can provide fast, efficient, and high quality designs.
- Field engineers can support you globally to provide onsite testing and verification of torsional vibration and stress.
6 Related Information
7 Related Services
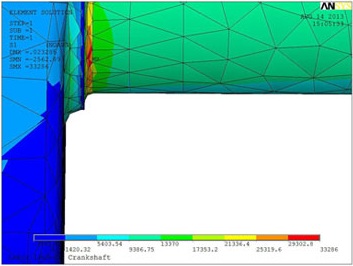 |
|
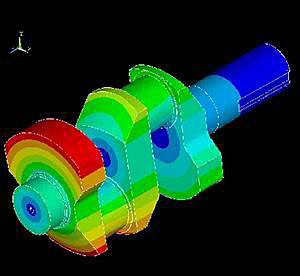 |
3D finite element analysis of a new crankshaft design – stresses at fillet of crank pin for bending and torsional loads
|
|
3D finite element analysis prediction of torsional displacement of a crankshaft
|
8 Key Words
Rotor dynamics
Understand the top three vibration threats in your piping system and how to tame them. Register now