Troubleshooting, Root Cause Analysis (RCA)
Advanced vibration analysis including pulsation, resonance, stress and transients
For more than 50 years, Wood has been known for reliable troubleshooting and RCA services expertise. Leading production operators call Wood to address vibration, pulsation, resonance, fatigue and performance issues (often called Advanced Vibration Analysis services).
Our focus includes compressors, pumps, engines, piping systems, gearboxes, and dynamics of foundations and structures. We identify the root cause of the problem and make immediate corrections when possible.
For more complicated issues, we apply our software modeling tools to simulate the problem and find the best solution. This approach has proven to be the quickest and most cost-effective method to fix problems and avoid expensive “trial and error” approaches.
Speak to a specialist
1 Applications
Typical applications include gas plants, compressor stations, liquid pumping stations, refineries, offshore production platforms, pipelines, paper mills, and water treatment facilities. Independent advice is often needed to address these issues:
- Component failure (broken piston, rods, gearbox, shaft, distance piece, bearings, etc.)
- Excessive pulsations in piping systems
- Mechanical, acoustical, structural, or torsional resonance in the system
- Improper skid and foundation design
- Installation problems including pipe strain
- Skid, foundation, and structural problems (dynamics)
- Valve problems
- Excessive noise
- Flow-induced or acoustic-induced vibration
- Slugging, two-phase flow, water hammer
- Performance problems
- Required supervision or turnkey support to implement improvements
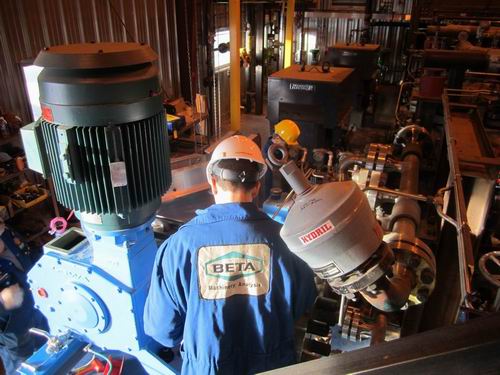 |
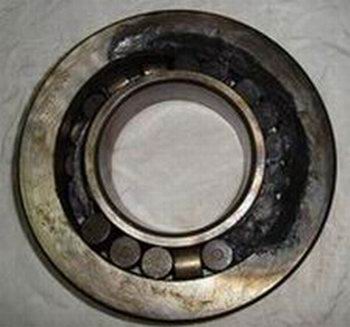 |
|
Compressor troubleshooting
|
Damaged bearing
|
Broken plunger pump
|
2 Scope
2.1 Troubleshooting
These problems often involve complex issues with many possible root causes. A methodical approach is needed to sift through these challenges and solve the underlying problem.
A field visit is often required to assess the problem, analyze the data, and prepare recommendations. For more complex problems a computer model or simulation is used to select and assess the optimal recommendation.
A unique methodology and approach has been developed for reciprocating compressors or pumps. These reciprocating assets create pressure pulsations and have other dynamic forces that require specialized analysis. Based on completing thousands of these field and design studies, Wood is the global leader in pulsation and vibration analysis – including time domain modeling software.
The scope may include these technical skills, depending on the machinery or piping problem:
- Vibration assessment on machines and piping systems
- Record vibration throughout the machine, skid, foundation and piping system. Wide range of diagnostic tools available – from single channel to over 100 channels using our data acquisition system. Proprietary software tools used in analyzing the complex data in an accurate and efficient manner.
- Evaluate vibrations at run speed, harmonic, and at non-synchronous frequencies.
- Identify locations where vibration exceeds the industry guideline.
- Measure vibration on turbomachinery Record shaft relative motion and/or casing vibration throughout a speed range and analyze using spectra, bode plots, shaft centerline plots, and envelope analysis to understand rotordynamic and bearing issues.
- Speed sweep For variable speed applications (motor or engine driven), check vibration amplitudes at all operating speeds – severe vibration at a specific speed due to resonant conditions is not uncommon.
- Pulsation assessment Measure pressure pulsations and identify locations where acoustical forces may be above guideline.
- Impact (bump) tests Measure mechanical natural frequencies (MNFs) of vessels, cylinders, frame, and other components of the system to identify where resonance will occur.
- Operating deflection shape (ODS) Measure relative vibration across the machine system –a useful technique to identify root cause(s) of problem.
- Foundation, skid check
- Inspect grout condition, relative vibration at different points on foundation, degradation, gravel/pile contact, and other factors affecting foundation integrity.
- Assess stiffness and resonance in skid and supporting structures.
- Strain gauging
- FIT, FIV, AIV or shell mode field analysis
- Performance review Computer simulation of system to verify that power and throughput meet specifications.
2.2 Root Cause Analysis (RCA)
A Root Cause Analysis (RCA) can be conducted when a more formal approach is needed for failure assessment, where the goal is to prevent recurrence by addressing the root cause of a problem. RCA is typically used as a reactive method of identifying event(s) causes and problems, and then resolving them. Analysis is done after an event has occurred.
Principles of Wood’s RCA service include:
- following a systematic analysis process;
- using a cross-functional team, including technical specialists;
- detailed inspection of failure information including components that have been preserved;
- interviewing staff who have knowledge of the failure and understand the operation and maintenance of the equipment;
- analysis of operating and maintenance data;
- application of a variety of structured RCA methods and approaches appropriate to the failure investigation;
- documentation of the RCA analysis process, analysis, conclusions and recommendations; and
- close interaction with the client to ensure resolution and implementation of findings.
The most important aspect in being able to perform a successful RCA is to preserve the failure evidence and to commence the RCA process as early as possible. If crucial evidence has been destroyed, it may not be possible to conclusively identify the failure mechanism and ultimate root cause.
_1.jpg) |
|
_2.jpg) |
Evaluating failed compressor components using Wood's Root Cause Analysis (RCA) Service |
3 Wood Advantages
Our experience plays a major role in the troubleshooting process. After being involved in thousands of projects we have unique tools, methods, and post processing techniques to improve the efficiency of our field investigations.
Advantages include:
- Audited safety program meets global standards. Focus on safety management is a significant advantage and benefit to our customers.
- Expert staff with unique troubleshooting skills. Largest team of trained experts in this field.
- Global support with offices in the USA, Canada, Asia and regular coverage in other areas.
- Specialized software analysis tools for fast and comprehensive results.
- Equipment calibration and testing. Most competitors lack resources for calibration of pulsation and vibration instrumentation.
- Track record in providing multi-year vibration contracts for owners.
- Long term customer relationships with large petroleum producers.
- Large inventory of diagnostic and troubleshooting tools (over a million dollars of test equipment and software tools) including many data acquisition systems (110+ channels of simultaneous data capture for complex troubleshooting assignments), data collectors, performance analyzers, various AC/DC transducers, signal processors, data profiling software, and performance assessment software.
4 Representative Experience
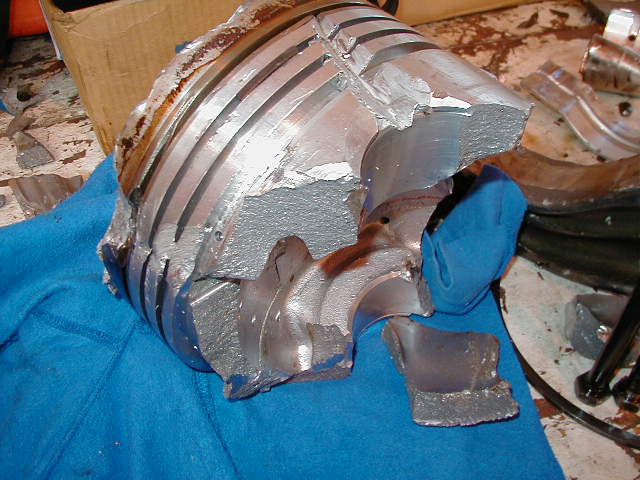 |
|
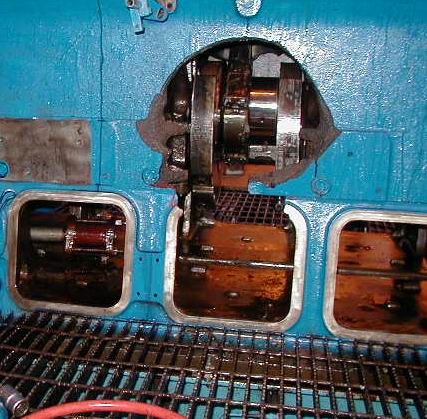 |
The cracked piston to the left caused the conrod failure (which came through the engine block)
|
- Reciprocating compressor Pulsation and Vibration Check. For a fleet of 50 compressors, Wood evaluated the pulsation control and mechanical design; and measured vibrations on the frame, vessels, piping, and skid. Advanced software and hardware tools, combined with expertly trained staff, enabled fast and accurate results. Specific improvements and recommendations were provided for each unit addressing resonance and piping vibration. We also provided support during implementation. This provided a significantly positive impact for the operator.
- Centrifugal compressor investigation A large gas plant was concerned about bearing life in a main centrifugal compressor and the ability to run for another year before a scheduled maintenance shutdown. Wood evaluated the vibrations and vibration and lube oil analysis history, and recommended continued operation with some additional monitoring. The unit ran the year and was then overhauled on a planned basis.
- Multi-unit site evaluation (Texas Gas Injection Facility) Wood conducted a field evaluation of an older gas injection facility with ten large compressors that had a history of vibration concerns. The field analysis recommended a number of repairs and modifications to pipe supports, compressor foundations and scrubber bases. Those recommendations resulted in a better mechanical condition. Wood also conducted a design pulsation study to reduce acoustic forces. The overall project resulted in much improved reliability.
- Paper mill speed trial A large scale paper mill was interested in speeding up production. Wood instrumented the paper machine with 88 channels of vibration and was able to identify a number of problem areas during a speed trial. Wood worked with the client and paper machine OEM to come to practical solutions and the paper machine has since successfully run to the higher speeds.
- Water treatment A waste water treatment plant had large vertical centrifugal displacement (VFD) pumps that regularly tripped on high vibration. Wood conducted a thorough field analysis and was able to identify a combination of torsional and lateral mechanical natural frequencies that were excited by blade pass frequencies at certain run speeds. A recommendation to change the number of vanes on the impellers was made. The client locked out the problematic speed ranges until the modifications were completed.
- Crankshaft failures Several fixed speed reciprocating compressors suffered crankshaft failures in Russia. Wood outfitted the packager’s representative with instrumentation and training and remotely diagnosed a torsional natural frequency problem. Wood’s design group conducted a design study and successful modification was completed in a cost effective and timely manner.
5 Related Services
6 Keywords
- Advanced vibration analysis
- Including pulsation, resonance, stress, transients, etc.
- Equipment failures
- Troubleshooting
- Root cause analysis
- Failures
- Rotating machinery problems
Understand the top three vibration threats in your piping system and how to tame them. Register now